GROVER ENGINEERING SOLVES THE RIDDLE
Faced with a major recall and the expense of replacing or repairing thousands of air compressors, a large manufacturer came to Grover Corporation for a solution…and we delivered.
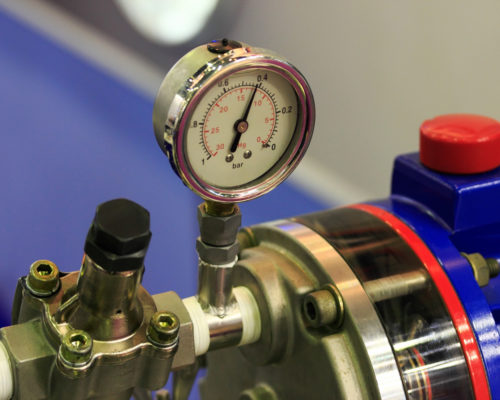
Challenge
A large manufacturer of piston air compressors contacted Grover Corporation asking if we would meet with their Engineering Department. Their Quality Department had recently identified that 4% of their piston air compressors in the market were experiencing an oil pass through rate higher than the maximum allowable 14 particles per million (ppm).
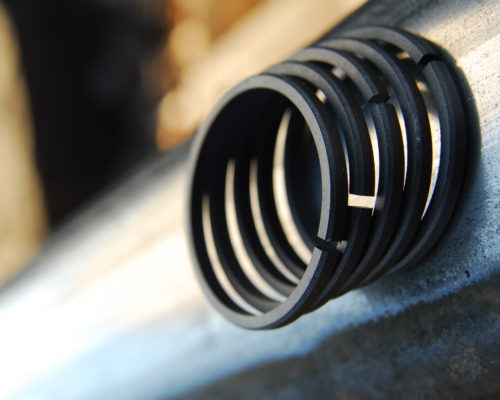
Solution
Grover’s engineers met with the Production, Quality and Engineering Departments to analyze the application. Each piston in the two-stage air compressor was using three taper face piston rings. Testing in stages, our engineers replaced one of the taper face piston rings with a butt cut taper face piston ring that featured a scraper groove.
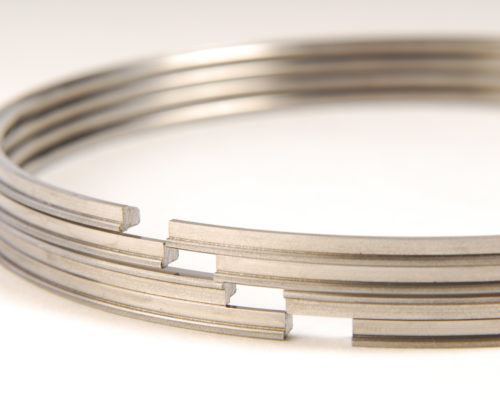
End-Result
When the new piston ring set design was used, oil pass through rate dropped from over 14 ppm to just 2 ppm.The customer was extremely impressed with Grover’s engineering and the final result it achieved. They were not only able to eliminate the expensive operation of re-honing the cylinder for the recalled air compressors, but also produced a better product!

Grover engineered a superior custom piston ring solution that was delivered with a short lead time.
